Turbo Tube Dryer
Historically, production of powdered detergents has been done either with spray drying equipment or with dry neutralization and agglomeration equipment. While spray dryers are versatile with respect to formulation and are capable of producing high active products, they are expensive to operate due to high energy costs, they require large capital expenses for equipment and land and create significant air pollution problems.. Production of powdered detergents by dry neutralization and agglomeration while utilizing inexpensive and compact equipment has severe formulation limitations. What has been required is a technology to produce concentrated, low moisture detergent actives which can be easily transported for later agglomeration into detergent powders.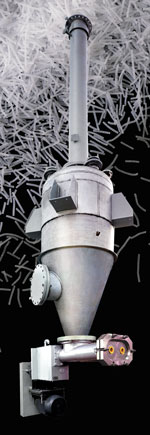
The net result is that total formulation versatility is achieved. The production of detergent active has been uncouple from the production of finished powdered detergents. The concentrated dry detergent active is available in powdered or non dusting needle form and can be easily and inexpensively shipped from large sulfonation facilities to small, local manufactures for formulation into finished products.
Incorporating the TTD into your existing detergent agglomeration process will greatly increase formulation flexibility by allowing much higher active levels than can be obtained by adding liquid surfactants or by dry neutralization of sulfonic acid. Mixed actives can be easily by dried and agglomerated into the finished detergent. In addition to surfactants, other liquid ingredients can be dried in the TTD prior to agglomeration.
Detergent Actives which can be dried:
- Alcohol sulfates
C12, C12/14, C14-15, C16,18, C12/18
- Alpha Olefin Sulfonate
C14/16
- Linear Alkylbenzene Sulfonate
C11-13
- MES
C12/14, C16/18
- SXS
- Mixed Anionic Detergent Actives
- Mixtures of LABS and liquid Silicates
The TTD has a number of advantages over traditional drying systems such as wiped film evaporators and spray towers:
- Lower capital and operating costs
- Energy efficient
- Non-dusting
- No moving parts
- No fire or explosion hazards
- No plume
- Compact
- Enhances spray tower and agglomerator capacities and efficiencies
- Self-cleaning
- No product degradation or loss during processing